2章 原料の調合と溶融炉
3章 成形器具と金型
4章 成形工程
5章 徐冷
1章 原料
(1)概要
多くの化学物質がガラス化する可能性を持っています。一般に無機物では、ケイ素(Si)、ホウ素(B)、ゲルマニウム(Ge)、リン(P)、ヒ素(As)などの酸化物が
主要なガラスを形成する物質です。これらの物質が溶融状態により急速に冷却されることにより結晶をつくることなく個体となりガラスが
得られます。
(2)化学成分によるガラスの分類
主なものは、ソーダ石灰ガラス、鉛ガラス、ホウケイ酸ガラスの各グループであり、この3つで全てのガラスの少なくとも95%を占めています。
①ソーダ石灰ガラス(工業的に生産されているガラスの大部分です。)
・・・・・・・窓用板ガラス、びん及び容器用ガラス等に使用されます。
その成分は、ケイ砂(酸化ケイ素,SiO2)が71~75%、ソーダ(酸化ナトリウム,Na2O,原料としてはソーダ灰すなわち炭酸ナトリウム,Na2CO3が使われる)が12~16%、石灰(酸化カルシウム,CaO,原料としては石灰石で主成分は炭酸カルシウム,CaCO3が使われる)が10~15%です。以上の主成分に着色剤などの特定の目的にあった原料が添加されます。
②鉛ガラス
・・・・・・・飲料用ガラス、花瓶、鉢、灰皿、装飾品などに使用されます。
酸化ケイ素(SiO2)が54~65%、酸化鉛(PbO)が18~38%、ソーダ(Na2O)もしくは酸化カリウム(K2O)が13~15%、その他若干の酸化物です(ドイツでは鉛含有量の低いガラス、PbO
18%未満はクリスタルガラスと呼ばれます)。
③ホウケイ酸ガラス
・・・・・・・化学工場の製造プラント、実験用ガラス器具、製薬産業のアンプルや薬びん、高輝度照明器具、家庭用耐熱用品等に使用されます。
酸化ケイ素(SiO2)が70~80%(非常に高い割合)、ホウ酸(B2O3)が7~13%、ソーダ(Na2O)もしくは酸化カリウム(K2O)が4~8%、酸化アルミニウム(Al2O3)が2~7%です。
④特殊ガラス(石英ガラス)他
・・・・・・・光学電気化学分野のさらに特殊な技術目的等に使用されます。
無水ケイ酸(SiO2)のみから成るガラスでシリカガラス、溶融石英などとも呼ばれています。熱膨張が非常に小さい。
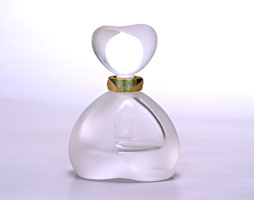
(3)原料の内容(びん、容器用ガラス)
①個々の原料
原料名 |
化学記号 |
用途 |
1.石粉(ケイ砂) (ケイ酸原料としてオーストラリア産フラッタリーサンドが使われる) |
ケイ酸(SIO2) 99.8% アルミナ(Al2O3) 0.04% 酸化鉄(Fe2O3) 0.008% |
主成分 |
2.ソーダ灰(炭酸ナトリウム) | Na2CO3 | 主成分 |
3.石灰石(炭酸カルシウム) | CaCO3 | 主成分 |
4.硼砂(ホウサ)(無水ホウ砂) | Na2B4O7 | 主成分 |
5.硝酸ソーダ | NaNO3 | 主成分 |
6.亜ヒ酸 | As2O3 | 主成分 |
7.二酸化マンガン | MnO2 | 色素(紫色、褐色、黒色) |
8.酸化アンチモン | Sb2O3 | 色素(赤色) |
9.酸化コバルト | CO3O4/CO2O3 | 色素(青/緑) |
10.光明丹(=鉛丹) | 四酸化三鉛 Pb3O4 | 機能(光沢、屈折) |
11.長石 カリ長石 ソーダ長石 灰長石 |
K2O・Al2O3・6SiO2 Na2O・Al2O・6SiO2 CaO・Al2O3・6SiO2 |
主成分 |
12.クレー粉(ろう石質粘土) | Al2O3源として | 色素(乳白) |
13.硝石(硝酸カリウム) | KNO3 | 機能(融剤、泡切剤) |
14.蛍石(フッ化カルシウム) | CaF2 | 色素(吹止) |
15.亜鉛華(酸化亜鉛) | ZnO | 色素[砡(ギョク)]、機能(融剤) |
16.鉛丹 | Pb3O4 | 機能(光沢、屈折) |
17.ケイフッ化ソーダ | Na2SiF6 | 色素(乳濁剤) |
18.硫酸バリウム | BaSO4 | 色素(乳白) |
19.水酸化アルミニウム | Al(OH)3 | 色素的機能(乳濁度) |
20.炭酸バリウム | BaCO3 | 機能(融剤、泡切剤) |
21.塩化ナトリウム | NaCl | 機能(泡切剤)、色素(乳濁剤) |
22.セレニウム(セレン) | Se | 色素(消色剤、ピンク色) |
23.重クロム酸カリウム | KHCr2O7 | 色素(青;ただし酸化、還元剤により大きく変わる) |
24.酸化銅 | Cu2O/CuO(第一/第二) | 色素(緑/淡青;第一/第二) |
25.ホウ酸 | H3BO4 | 機能(硬質) |
26.硫酸銅 | CuSO4・5H2O | 色素(淡青) |
27.酸化クローム | Cr2O3 | 色素(緑) |
28.硫黄華 | S | 色素(赤、ピンク色) |
29.硫化カドミウム | CdS | 色素(ピンク色、黄色) |
30.炭粉(カーボン) | C | 色素(黒、褐色、黄色) |
31.アンチモン(生アンチ) | Sb | 機能(泡切剤) |
32.酸化ニッケル | NiO | 色素(消色剤、ピンク色、紫色) |
33.骨灰(リン酸カルシウム) | Ca3(PO4)2 | 色素[砡(ギョク)] |
34.炭酸カリウム | K2CO3 | 色素(消色剤、紫色) |
35.硝酸カリウム | KNO3 | カリウム源、色素 |
36.亜鉛末 | Zn | 色素(赤) |
37.炭酸マグネシウム | MgCO3 | 主成分(溶融剤) |
38.炭酸リチウム | Li2CO3 | 機能(融剤) (泡切、光沢) |
39.重炭酸ナトリウム | NaHCO3 | 色素(茶) |
40.弁柄(酸化鉄赤) | FeSO4・7H2O | 色素(茶) |
41.酸化鉄 | Fe2O3 | 色素(黒、茶) |
42.芒硝(ボウショウ) | Na2SO4 | 機能(バリ止)、色素(乳濁) |
43.硫黄 | S | 色素(茶) |
44.銅糀 | (Cu) | 色素(水色) |
45.酸化第一錫 | SnO | 色素(銅赤)、機能(還元剤) |
46.リン酸アンモニウム | (NH4)3PO4 | 色素(黄色) |
47.酒石酸カリウムソーダ | C4H4O6・KNa・4H2O | 色素(赤)、機能(還元剤) |
48.酸化アルミニウム(アルミナ) | Al2O3 | 色素(乳白) |
49.金 | Au | 色素(紅色) |
50.ドロマイト(白雲石) | Ca・Mg・(CO3)2 | 主成分(溶融剤) |
51.酸化セリウム | CeO2 | 遮蔽ガラス原料、色素(黄) |
②色別適用原料
色名 |
原料名 |
化学記号 |
砡(ギョク)(Opal) | 蛍石(フッ化カルシウム) 氷晶石(ケイフッ化ソーダ) 骨石(リン酸カルシウム) クレー粉(アルミナ) 硫酸バリウム |
CaF2 Na2SiF6 Ca3(PO4)2 Al2O3 BaSO4 |
乳白 | 氷晶石(ケイフッ化ソーダ) 酸化アルミニウム(アルミナ) 水酸化アルミニウム 亜鉛華(酸化亜鉛) 硫酸バリウム |
Na2SiF6 Al2O3 Al(OH)3 ZnO BaSO4 |
黄色 | 塩化銀 硫酸カドミニウム 二酸化マンガン 酸化ウラン 硫黄 クロム酸カリウム 酸化セリウム 酸化チタン 炭素 |
AgCl CdS MnO2 UO,UO2 S K2Cr2O7 CeO2 TiO2 C |
ピンク | 硫黄(未、華) 二酸化マンガン 亜鉛華(酸化亜鉛) 硫化カドミニウム セレン 亜セレン酸ソーダ |
S MnO2 ZnO CdS Se Na2SeO |
赤 | 酸化第一銅 酸化第一錫 セレン 亜セレン酸ソーダ 硫化カドミニウム 硫黄(未、華) 酸化アンチモン 亜鉛華(酸化亜鉛) 金 酸化ネオジウム 酒石酸カリウムソーダ |
Cu2O SnO Se Na2SeO3 CdS S Sb2O3 ZnO Au Nd2O3 C4H4O6・KNa・4H2O |
茶 | 酸化第二鉄 二酸化マンガン 硫黄 硫化カドミニウム 酸化第一銅 重クロム酸カリウム 炭素 硫化鉄 |
Fe2O3 MnO2 S CdS Cu2O KHCr2O7 C FeS |
青 | 酸化コバルト 酸化第二銅 酸化第一鉄 硫酸銅 クロム酸カリウム 重クロム酸カリウム |
Co3O4 CuO Fe3O4 CuSO4・5H2O K2Cr2O7 KHCr2O7 |
緑 | 二酸化マンガン 重クロム酸カリウム 酸化第一鉄 酸化第一銅 酸化クローム 酸化コバルト 酸化バナジウム クロム酸カリウム 酸化プラセオジム |
MnO2 KHCr2O7 Fe3O4 Cu2O Cr2O3 Co3O4 V2O5 K2Cr2O7 Pr2O3 |
紫 | 二酸化マンガン 酸化第一鉄 酸化モリブデン 酸化コバルト 酸化ニッケル 酸化タングステン 酸化ネオジム |
MnO2 Fe3O4 MoO Co2O3 NiO WO Nd2O3 |
黒 | 二酸化マンガン 重クロム酸カリウム 酸化コバルト 酸化ニッケル 酸化第二鉄 酸化第一銅 酸化鉛 炭素 |
MnO2 KHCr2O7 Co3O4 NiO Fe2O3 Cu2O3 PbO C |
2章 原料の調合と溶融炉
(1)原料調合
調合においては各製造工場で異なりますが、一般に透明ガラスについては1章の(3)-①「個々の原料」の1.~9.までの調合です。色ガラスは特色を除いてこの透明ガラス調合にそれぞれの色素を調合していくわけで、これには前記の色別摘要原料も参考となりますが、各工場により秘密データとなってはいます。
尚、ガラス主原料に対して言われている副原料とは、融剤、消色剤、清澄剤(泡切剤)、酸化剤、還元剤、着色剤、乳濁剤等があって、一原料で色々な副原料の役目をしているものがあります。
代表的な色調合は次のとおりです。
① 透明ガラスの場合(1章(3)-①の項目)
1、2、3、4、5、6、7、8 & 9
② 黒色ガラスの場合
1、2、3、4、7、8、9に二酸化マンガン、酸化コバルトを多量に使用します。
③ 乳白ガラスの場合
1、2、3、4、7、8、9にケイフッ化ソーダ、塩化ナトリウム等を使用します。
④ 砡(ギョク)ガラスの場合
1、2、3、4、7、8、9に蛍石、ケイフッ化ソーダ、クレー粉等を使用します。
⑤ ブドウ色ガラスの場合
二酸化マンガンを多量に使用します。
⑥ コバルト系色ガラスの場合
酸化コバルトを使用します。
⑦ ピンク系色ガラスの場合
セレニウム等を使用します。
⑧ 黄色系ガラスの場合
硫化カドミウム、硫黄華等を使用します。
⑨ 赤系ガラスの場合
セレニウム、硫化カドミウム、アンバ(C+S系)を使用します。
⑩ 茶系ガラスの場合
硫黄化、炭粉等を使用します。
尚、詳細については1章(3)-②「色別適用原料」を参照してください。
また、中間色については、その色素の量を加減することにより対応できますが、高温溶融のため熱によって変色する場合があり、調合溶融度が非常に難しい。
(2) 溶融炉[坩堝窯(るつぼがま)]および坩堝(るつぼ)の機構
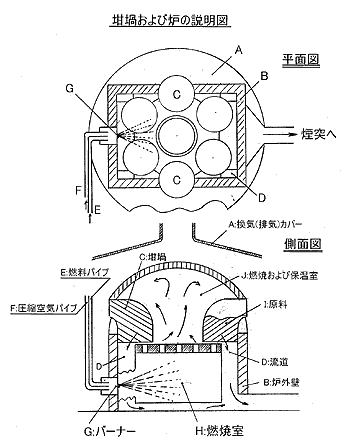
① 摘要
坩堝窯は耐火煉瓦の内壁、シリカ煉瓦の丸天井(クラウン)、および断熱煉瓦の外壁で構成されます(坩堝および炉の説明図のB部)。坩堝窯は通常、燃料ガスの予熱を行なう下部と、坩堝を設置する溶融室としての上部に分けられます。今日、手巻き成形に使われる坩堝窯は12個程度までの坩堝を収める室があり、それぞれ異なった種類のガラスを溶融することが出来ます。窯の寿命は1~3年です。
坩堝は耐火粘土で作られ、[時にはシリマナイト煉瓦の粗粒(グロッグ)を混入して]、ガラスの溶融に使用する前に1,000℃までゆっくりと予熱されます。
坩堝の可能容量は最大2,000kgであって、普通は100~500kgのものが使用されています。坩堝の平均寿命は原料により異なりますが約8週間です。(透明ガラスでは4~6週間です。)
坩堝窯は絶えず加熱されていますが、その温度は変化しています。バッチは夕方に坩堝に供給され、夜間に溶融され、朝早く成形が開始されます。溶融温度はガラスの種類によって異なり1,300℃~1,600℃であって、ガラスを取り出し成形する団塊では窯の温度は900℃~1,200℃とされています。坩堝溶融は一般にガラス種が1交替分しか続かないため、24時間操業には適しません。
② 作動原理
坩堝および炉の説明図でEより送られてくる燃料とFより導入された圧縮空気で気化され(霧状になる)、噴出させます(現在燃料はほとんどが重油である)。
Gで気化し噴出したガスはHで燃焼し、J(燃料および保温室)で循環流れとなり、Dを通って排出されます。
原料Iの入った坩堝Cは同室にあり1,000℃~1,500℃まで加熱され原料が溶融されます。また、坩堝が破損した場合や、バッチがこぼれて坩堝の外へ「たね」が流出してきた場合、図のD(流動)に「たね」が流れるようになっています。
3章 成形器具と金型
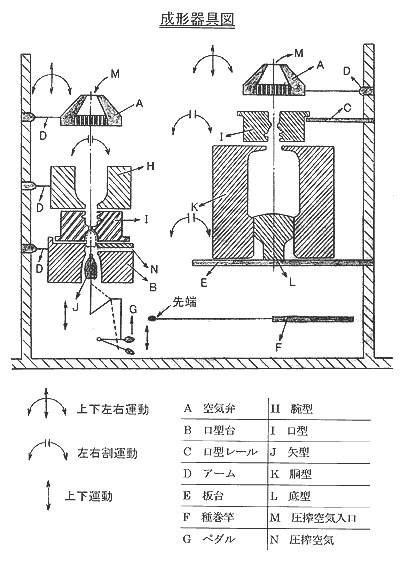
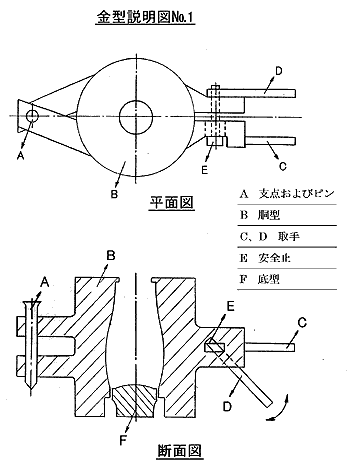
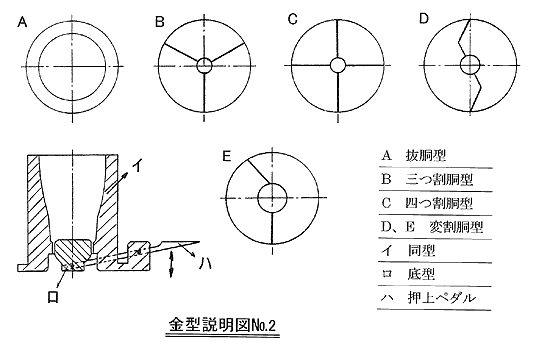
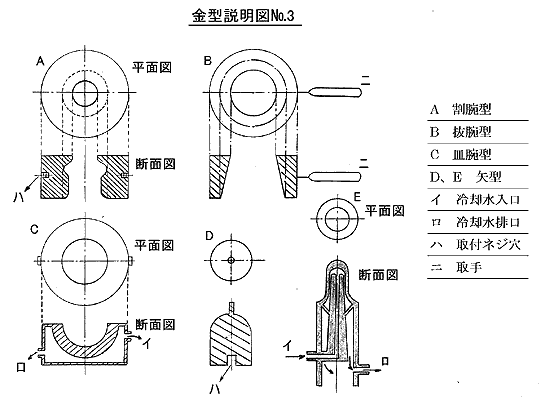
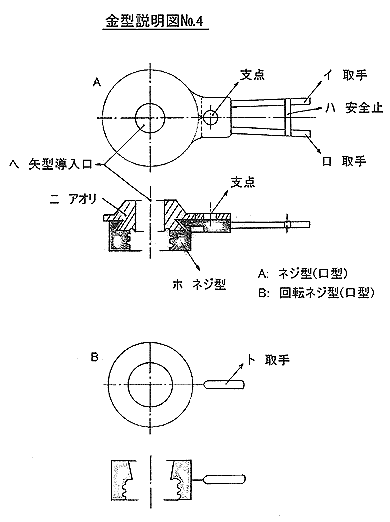
(1) 概要
手巻き成形で特に容器用の成形金型はガラス瓶のデザインと製造工程により異なるが金型を大別すると次の通りとなります。腕型(ワン型) | 抜腕型 割腕型 皿腕型 |
金型説明図№3 B参照 金型説明図№3 A参照 金型説明図№3 C参照 |
口型(ネジ型) | 回転ネジ型 割ネジ型 |
金型説明図№4 B参照 金型説明図№4 A参照 |
胴型 | 割型 2つ割型 3つ割型 4つ割型 変割型 抜型 |
金型説明図№1 参照 金型説明図№2 B参照 金型説明図№2 C参照 金型説明図№2 D~E参照 金型説明図№2 A参照 |
矢型 | 金型説明図№3 E参照 | |
底型 | (これは胴型に附帯されている) | 金型説明図№1 参照 |
成形器具図は金型とそれを作動させる器具等を示したものであり、矢印の方向が金型及び器具の動作方向を表しています。
手巻き成形の金型は独特のもので、それなりの歴史伝道があり、高熱による危険性、温度調節の微妙さや色調の難しさ、および成形操作の高度な熟練度等、大変難易度の高い製造分野です。
(2) 金型詳細説明
① 胴型
a) 取り扱いならびに作動構造
割型の場合、2つ割型、3つ割型、4つ割型および変割型のいずれにおいても取り扱い、ならびに作動構造は同じです。ガラスびんのデザインにより2つ割ではガラスびんの表面の凹凸により困難となる場合、3つ割とします。さらに3つ割でも困難な場合は4つ割とします。
これらは単割の場合は支点中心としての金型の運動なのですが、複割の場合は金型中心が運動の中心にほぼ一致してくるので凹凸の抜きが可能となるわけです。
変割の場合はまれに見られるもので、製品の正面に合わせ目がくるような場合、ガラスびんのデザインのために合わせ目を特定される場合ならびに表面につける模様が彫刻されている場合等、正割が困難である場合に用いられます。
b) 取り扱い方法 ( 金型説明図№1を参照ください。)
取手Dを水平の位置にすることにより型開きが可能になります(DはEに連動されており水平にすることにより型開きが可能になり垂れ下げることにより型締、ならびに安全装置が施されます)。型開動作はDを水平の位置にして、C・Dを各々左右に動かすことによりAを中心として、Bが開かれます。この場合もFが半固定であるため同じ位置にあります。
型閉の場合でも、この下が半固定であるために同じ位置に戻すことが出来ます。型閉後Dを下げます。この操作は抜型を除いて、3つ割・4つ割・変割と全て同じです。
c) 抜型
抜型は構造が非常に簡単であり、金型の寿命を長くします。また、割型と違って合わせ目がないのが特徴であり、利点でもあります。しかしながらガラスびんのデザインに対しての条件として製品の上部が下部より太いことが要求されます。そして模様、額等をつけることは出来ません。
成形方法は割型と同じですが、型出し(金型より製品を取り出すこと)が型を割らず、金型説明図№2の「ハ」のペダルを押し下げることによって製品が押し上げられ、取り出しが可能となります。
② 腕型(割型)( 金型説明図№3を参照ください。)
図の中、「A」(割腕型)の「ハ」は成形器具に取り付けるネジ穴であって、割腕の操作は成形器具のペダルによって左右に動くことになります。Bは前述した胴抜型とよく似ており、この操作は取手「ニ」で行ないます。胴抜型の操作は製品を押し上げましたが、その腕型では型を抜き取るので、製品の上部より下部の方が太いことが条件となります。
③ 皿型( 金型説明図№3を参照ください。)
図の中、「C」は前述の腕型とは成形方法が異なります。これは一般に半押し成形専用腕型と言います。この成形方法は種巻竿より得たガラスをこの皿腕の中に切り落とし、この腕の中に口型をのせ、さらに矢を差し下して成形します。圧迫式型の矢型、口型、腕型の順位と正反対となります。
図の中、「イ」および「ロ」は腕型の焼き過ぎを防ぐための冷却水等の入口と排出口です。
④ 矢型 ( 金型説明図№3を参照ください。)
図の中、「D」は一般の矢型であって、「ハ」は取り付けネジ穴です。この先端の突起部の太さ(径)がガラスびんの口内径に相当する部分で、口径との関係を十分考慮しなければいけません。「E」は、特殊な半押式型専用の矢型であって、焼き過ぎを防ぐため冷却水循環パイプが内装されています(ごく限られたタイプです)。
⑤ ネジ型(口型) ( 金型説明図№4を参照ください。)
図の中の「A」は割型で「ニ」の部分が環状になっていて、「ホ」の部分が左右に割れるものが多い。「イ」および「ロ」が取手で、これを左右に動かすことにより「ホ」に切ってあるネジ山の部分が左右に開割されます。図の支点は「イ」、「ロ」および「ニ」の三つの支点となっています。
「ハ」は「イ」に固定され、「ロ」型を閉めた状態での安全装置の役目をしている。また、「ヘ」の開口部が矢型の導入口です。
4章 成形工程 ( 成形器具図 を参照ください。)
(1) 種巻(たねまき)
図の下(種巻竿)を使って坩堝より種を巻き取り、「H」(腕型)へ垂落させます。(この操作は成形工程中最高の技術を要します)。また、この場合、ガラスの量は種巻者の感覚一つで安定化させています。
(2) 種切り、および成形
種巻竿より垂落された「種」を成形者[俗に切者(きりや)と言う]が分量を感覚で決め、「H」(腕型)へ、はさみを使って切り落とします。この場合、成形者は「G」(ペダル)を踏み下げ、「J」(矢型)を図の点線の位置に置きます。「H」(腕型)に切り落とされた種は先に口型の部分を成形するため圧縮空気を「H」上部より導入、圧迫させます。この場合の動作は「A」(空気弁)に連接しているペダルで「H」(腕型)に接圧させると、「A」に内装されている弁が開き空気が導入されます。次に、踏み下げられていた「G」(ペダル)を離し、「N」より圧縮空気を入れ、ガラス容器内部の空間の「あらまし」を成形します。その後、「H」にガラスを原型金型(胴型部)へ移します。
この移行作業は先に成形されている口部の口型をもって上下を逆にして行ないます。
これは、「H」での成形から通常の逆となっているので、原型金型で仕上げるときには、また逆にします(正常位に戻す)。
「C」(口型レール)は中空状態のガラスを挟んだ「I」(口型)をセットするレールです。セットする前に「K」(胴型)は支点の元で左右に割離されており、口型がセットされれば「K」を元の位置に閉合させます。次に「M」(圧縮空気入口)を「I」に接圧させ、圧縮空気を導入して成形します。
成形後「I」(口型)ならびに「K」(胴型)を割離して製品を取り出します。
この作業をする者を俗に出者(だしや)と言います。
最後に手巻成形の方法として次のものがあります。
・圧迫成形 圧縮空気で成形する方法
・半押成形 圧迫とプレスの二つを取り入れた方法
・押切成形(プレス成形) 空気を使わず金型と金型の接圧で行なう方法
5章 徐冷
成形後のガラスは短時間で温度降下があるため、残留歪が発生しています。これをそのままにしておくと大きな応力によりショックを与えなくても瞬間的に破損してしまいます。
したがって成形方法の如何を問わず、必ず徐冷(再加熱させ、徐々に冷却させる)は行なわれます。その方法は時間をかけた処理作業で、徐冷炉が使われます。
徐冷炉には次のものがあります。
・本冷(ほんざまし)
・送り冷(おくりざまし) 直接法
・送り冷(おくりざまし) 間接法(マックル型)
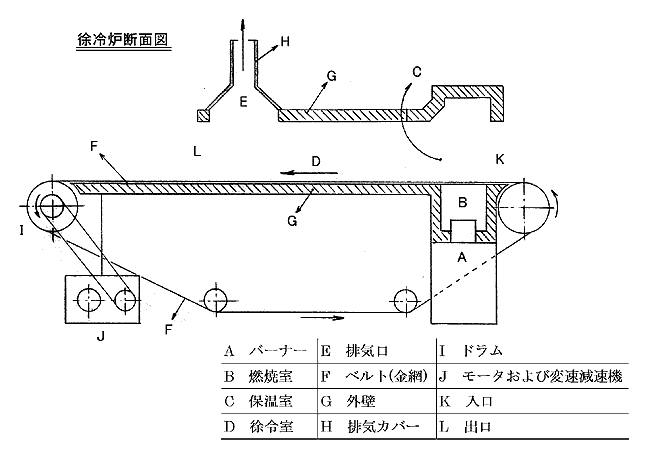
(1) 本冷(ほんざまし)
この方法は現在ほとんど使われていませんが、製品の歪検査規格が厳しいものや、製品そのものが非常に大きい場合(例えば、ガラスの肉厚が著しく、一般のガラス容器類のサイズをはるかに超えた大型のもの)には必要です。徐冷は成形したものを、室に納め必要に加熱した後、冷却するまで密閉して置いておきます。密閉期間は短くして1日、長くて10数日に及ぶこともあります。
なお、この室の材質は耐火、保温煉瓦が用いられており、空気膨張のための機構は必要としません。
(2) 送り冷(おくりざまし)( 徐冷炉断面図 を参照ください。)
図のとおり、コンベアー方式を採用した能率的かつ合理化された最近の方法です。コンベアー入口の「K」にガラス製品を並べて置き、「B」の燃料室の上と「C」(保温室)、「D」(徐冷室)を通って「L」(出口)に搬送されます。この時点でほとんど冷却されており、検査、箱詰が可能な段階です。徐冷で直接型、間接型共に同じ流れ方であるが、直接型は「B」、「C」にそれぞれ燃焼状態が見られ、場合により製品は?(ほのお)が直接当たります。そのため表面に白い粉末状の付着が見られます(水洗いで簡単に取り除くことはできますが一つの欠点です)。
間接法は「B」と「C」がはっきり区別されているので外面から焔(ほのお)を見ることはできませんし、製品は成型された時と同じでガスによる付着物は全くありません。
徐冷温度は400℃~600℃が普通であり、徐冷時間は約100分です。